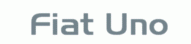
Fiat Uno Manual
Engine - 999 and 1108 cc (FIRE)Supplement: Revisions and information on later models / Engine - 999 and 1108 cc (FIRE)
Note: Later models are fitted with SPi fuel injection. Where a procedure refers to a carburettor, if applicable, replace with throttle body.
PART A: GENERAL
Description
1 Both of these engine types are designated
FIRE (Fully Integrated Robotised Engine),
being largely manufactured and assembled by
computer-controlled mechanical robots.
2 The engine is of oversquare design, having four cylinders and a belt-driven overhead camshaft.
3 The high torque of this engine enables higher gear ratios to be used with the result that fuel economy is exceptionally good.
4 The cylinder head is of light alloy, while the cylinder block is cast-iron.
5 The camshaft is supported in three bearings which have detachable caps.
6 Valve clearances are maintained by shims located in the cam followers (tappets).
7 The cylinder head is of crossflow type having the intake manifold (coolant-heated) and exhaust manifold on opposite sides.
8 The pistons have two compression rings and one oil control ring and are connected to the connecting rods by means of a gudgeon pin which is an interference fit in the rod small-end.
9 The crankshaft is supported in five main bearings. The upper section of the centre bearing shell retains semi-circular thrust washers to control crankshaft endfloat.
10 The oil pump, which is of gear type, is mounted on the front end of the crankshaft and driven by it.
11 The flexible toothed timing belt drives the camshaft and the coolant pump from a sprocket on the front end of the crankshaft.
The belt is tensioned by an eccentrically-mounted pulley.
12 The distributor and the fuel pump (carburettor models) are driven from the flywheel end of the camshaft. The fuel pump on fuel injection models is an integral unit combined with the fuel gauge sender unit and immersed in the fuel tank.
Fig. 13.2 Cross-section view of the 999 and 1108 cc engine (Sec 5A)
Fig. 13.3 Longitudinal sectional view of the 999 and 1108 cc engine (Sec 5A)
Fig. 13.4 999 and 1008 cc engine lubrication system (Sec 5A)
PART B:
OPERATIONS POSSIBLE
WITH ENGINE IN CAR
Valve clearances - adjustment
1 The operations are similar to those
described in Chapter 1, Section 26, but note
that the special tools referred to have different
part numbers for the FlRE engine -
1860443000 and 1887001000 (photos).
5B.1A Checking a valve clearance
5B.1B Using a modified C-spanner and screwdriver to remove a shim
2 Remember that the clearance for inlet and exhaust valves differs see Specifications at the beginning of this Supplement.
3 Counting from the timing cover end of the engine, the valve sequence is as follows.
Inlet 2-4-5-7
Exhaust 1-3-6-8
Timing belt - renewal
4 Remove the air cleaner.
5 Slacken and remove the alternator drivebelt, then remove the spark plugs.
6 Unbolt and remove the timing belt cover.
Note the bolt located at the bottom of the cover, this can be easily overlooked (photo).
5B.6 Timing cover lower fixing bolt removal
7 Unbolt and remove the crankshaft pulley (photo).
5B.7 Unscrewing the crankshaft pulley bolts
8 Turn the crankshaft sprocket bolt, or engage top gear and raise and turn a front roadwheel, until the camshaft sprocket TDC timing mark is aligned with the mark on the cylinder head and the crankshaft sprocket timing mark is aligned with the mark on the oil pump cover (photos).
5B.8A Camshaft sprocket timing mark and cylinder head timing mark in
alignment
5B.8B Crankshaft sprocket timing mark and oil pump cover alignment mark
(arrowed)
9 Release the nut on the timing belt tensioner, move the pulley away from the belt and retighten the nut to hold the pulley in the retracted position (photo).
5B.9 Releasing the timing belt tensioner nut
10 Slide the drivebelt from the sprockets.
11 When refitting the new belt, make sure that the sprocket timing marks are still in alignment and fit the belt so that the arrows on the belt point in the direction of engine rotation, and the lines of the belt coincide with the sprocket marks.
12 Engage the timing belt with the crankshaft sprocket first, then place it around the coolant pump sprocket and the camshaft sprocket (photo). Finally slip the belt around the tensioner pulley.
5B.12 Fitting the timing belt
13 Release the tensioner nut and push the pulley against the belt until the belt is quite taut. Check that the sprocket timing marks have not moved out of alignment. If they have, reset them by moving them over the belt teeth.
14 Still applying force to the pulley, tighten its nut.
15 Turn the crankshaft through two complete turns in the normal direction of rotation and check that when the centre of the longest run of the belt is gripped between finger and thumb it can just be twisted through 90º. If increased tension is required to achieve this, release the tensioner nut and prise the pulley against the timing belt. Note: The above procedure serves only as a rough guide to setting the belt tension having it checked by a FIAT dealer at the earliest opportunity is recommended.
16 Refit the timing belt cover, the crankshaft pulley, alternator drivebelt, spark plugs and the air cleaner.
Camshaft -
removal and refitting
Warning: Refer to the beginning
of Section 9 before starting any
work.
17 Remove the air cleaner and the fuel pump (carb. models), as described in Section 9 of this Supplement.
18 Remove the distributor (Section 10).
19 Remove the timing belt cover.
20 Unbolt and remove the camshaft cover, having first disconnected the HT lead clip (photos).
5B.20A Camshaft cover HT lead clip
5B.20B Removing the camshaft cover
21 Turn the crankshaft (by engaging top gear and raising and turning a front roadwheel) until No. 4 piston is at TDC. The timing mark on the camshaft sprocket will be in alignment with the mark on the cylinder head.
22 Pass a rod through one of the holes in the camshaft sprocket to prevent it rotating and then unscrew the sprocket fixing bolt. Slip the sprocket from the camshaft and out of the loop of the belt (photos).
5B.22A Unscrewing the camshaft sprocket bolt
5B.22B Camshaft sprocket bolt and washer
5B.22C Camshaft sprocket showing integral key (arrowed)
23 Mark the camshaft bearing caps as to position and then unbolt and remove the lubrication pipe (prise the oil feed stub out with a screwdriver), unscrew the remaining bolts and take off the bearing caps (photos).
5B.23A Prising out the camshaft oil feed pipe stub
5B.23B Unscrewing the camshaft bearing/banjo union bolt
5B.23C Camshaft lubrication pipe
5B.23D Camshaft bearing cap showing short and long positioning dowels for
correct fitting
24 Lift the camshaft carefully from the cylinder head, checking that the valve clearance shims and cam followers are not withdrawn by the adhesion of the oil (photo).
5B.24 Removing the camshaft
25 If the shims and cam followers are to be removed, keep them in their originally fitted order (photos).
2B.25A Valve clearance shim showing thickness mark
5B.25B Removing a cam follower (tappet) with shim
26 Refitting is a reversal of removal but use a new camshaft oil seal and camshaft cover gasket. Oil the camshaft bearings (photos).
5B.26A Camshaft oil seal
5B.26B Camshaft cover gasket
27 Make sure that the timing belt is reconnected and tensioned as described previously.
28 Check the valve clearances.
29 Tighten all nuts and bolts to the specified torque.
Cylinder head -
removal and refitting
Warning: Refer to the beginning
of Section 9 before starting any
work.
Note: The cylinder head should be removed cold.
30 Drain the cooling system.
31 Remove the air cleaner.
32 Disconnect the throttle and choke connections from the carburettor (photo).
5B.32 Disconnecting the throttle cable
33 On carburettor models, disconnect the fuel hoses from the fuel pump and the carburettor. On fuel injection models, depressurize the fuel system, before disconnecting the fuel pipes and removing the throttle body, as described in Section 9D.
34 Disconnect the coolant and vacuum hoses from the cylinder head and inlet manifold (photo).
5B.34 Inlet manifold coolant hose (A) and brake servo vacuum hose (B)
35 Disconnect the electrical lead from the coolant temperature switch, the LT leads from the distributor and the idle cut-off solenoid lead.
36 Remove the distributor cap, disconnect the plug leads and place the cap and leads to one side of the engine compartment.
37 Unbolt and remove the timing belt cover.
38 Set No. 4 piston to TDC and then release the timing belt tensioner and slip the belt from the camshaft and coolant pump sprockets.
39 Unbolt and remove the inlet manifold, complete with carburettor, or throttle body as applicable.
40 Unbolt the exhaust manifold from the cylinder head and tie it to one side of the engine compartment; the downpipe bracket will have to be disconnected.
41 Unscrew the cylinder head bolts, a half turn at a time in the reverse order to that shown in Fig. 1.30 of Chapter 1. When the bolts are free, remove them with their washers.
42 Lift the cylinder head from the block. If it is stuck tight, insert pieces of wood into the exhaust or inlet ports and use them as levers to “rock” the head off the block. On no account drive levers into the gasket joint or attempt to tap the head sideways as it is located on positioning dowels.
43 Remove and discard the cylinder head gasket and both manifold gaskets.
44 The cylinder head can be dismantled after removing the camshaft and cam followers as described in the preceding sub-Section.
45 Further dismantling and decarbonising are described in Chapter 1, Section 39. Note that single valve springs are used.
46 If the valves have been ground in, the valve clearances will require adjusting, as described previously. This should be done before the cylinder head is refitted to the engine.
47 Before refitting the assembled cylinder head, make sure that the head and block mating surfaces are perfectly clean, and that the block bolt holes have been cleared of any oil.
48 The camshaft sprocket timing mark must be aligned with the one on the cylinder head.
49 The new gasket should not be removed from its nylon cover until required for use. Fit the gasket dry to perfectly clean surfaces.
50 Place the gasket on the cylinder block so that the word ALTO can be read from above (photos).
5B.50A Cylinder head gasket
5B.50B Cylinder head gasket top surface marking
51 Lower the cylinder head onto the block so that it locates on the positioning dowels (photo).
5B.51 Fitting the cylinder head
52 The cylinder head bolts must have clean threads, dipped in engine oil and allowed to drain for thirty minutes. Screw the bolts in finger-tight and then tighten them in the sequence shown in Fig. 1.30 of Chapter 1, and in the stages specified (see Specification) (photos).
5B.52A Inserting a cylinder head bolt
5B.52B Typical disc for angular tightening of cylinder head bolts
53 Refit the inlet manifold and carburettor using a new gasket.
54 Reconnect the exhaust manifold using a new gasket. Tighten all nuts to the specified torque. Reconnect the exhaust downpipe bracket.
55 Reconnect the timing belt and tension it as described earlier.
56 Refit the timing belt cover and the distributor cap and camshaft cover.
57 Reconnect all hoses, electrical leads and controls.
58 Fit the air cleaner.
59 Fill and bleed the cooling system.
Sump pan -
removal and refitting
60 Drain the engine oil.
61 Unbolt and remove the cover plate from the lower part of the flywheel housing (photo).
The two lower bolts retain the gearchange rod support strut.
5B.61 Removing the flywheel housing cover plate
62 Unscrew the sump pan securing screws and pull the sump pan downwards to remove it (photo). The joint sealant will require cutting with a sharp knife to release the pan. Clean away all old gasket material.
5B.62 Removing the sump pan
63 A bead 3.0 mm in diameter of RTV silicone instant gasket should be applied to the sump pan flange and then the pan offered up. Screw in the fixing screws and tighten to the specified torque. Note the flange end fixing screw nuts (photos).
5B.63A Tightening a sump pan screw
5B.63B Sump pan flange end fixing screw and nut
64 Wait one hour before filling with engine oil.
65 Refit the flywheel housing cover plate.
Oil pump - removal,
checking and refitting
66 Drain the engine oil and remove the sump
pan as described in the last sub-Section.
Unscrew and remove the oil filter cartridge.
67 Remove the timing belt.
68 Lock the crankshaft against rotation either by placing a block of wood between a crankshaft web and the inside of the crankcase or by jamming the flywheel starter ring gear with a suitable tool.
69 Unscrew and remove the crankshaft sprocket bolt and take off the timing belt sprocket. If it is tight, use two screwdrivers to lever it off or use a two- or three-legged puller.
70 Unbolt and remove the oil pick-up/filter screen assembly. Note the sealing washer.
71 Extract the oil pump fixing bolts and withdraw the pump.
72 The oil pump incorporates a pressure relief valve which can be removed for examination by depressing the spring plunger and pulling out the keeper plate (photos).
5B.72A Removing the oil pump relief valve keeper plate
5B.72B Oil pump relief valve components
73 If pump wear is suspected, check the gears in the following way. Extract the fixing screws and remove the rear cover plate. The screws are very tight and will probably require the use of an impact driver to release them (photo).
5B.73 Removing the oil pump rear cover plate screws
74 Check the clearance between the outer gear and the pump housing using feeler blades, and also the gear endfloat by placing a straight-edge across the pump body and checking the gap between the straight-edge and gear face. If the clearances are outside the specified tolerance, renew the oil pump complete (photos).
5B.74A Checking the oil pump gear-tohousing clearance
5B.74B Checking the oil pump gear endfloat
75 If the pump is unworn, refit the rear cover plate and tighten the screws fully.
76 Apply air pressure from a tyre pump to the oil pump oil ducts to clear any sludge or other material and then prime the pump by pouring clean engine oil into its intake duct at the same time turning the oil pump inner gear with the fingers.
77 Lever out the oil seal and drive a new one squarely into the oil pump casing (photos).
5B.77A Removing the oil pump seal
5B.77B Using a socket to fit the new oil pump oil seal
Lubricate the oil seal lips.
78 Bolt the pump into position using a new joint gasket. Note one bolt is longer than the others (photo).
5B.78 Fitting the oil pump
79 Bolt on the oil pick-up assembly using a new sealing washer.
80 Fit the crankshaft sprocket and tighten the bolt to specified torque.
81 Fit and tension the timing belt.
82 Fit the sump pan. Screw on a new oil filter cartridge. Wait for the specified period of time (one hour) and then fill the engine with oil.
83 Run the engine for a few minutes, then check and top up the oil level.
Pistons/connecting rods -
removal and refitting
84 Remove the sump pan.
85 Unbolt and remove the oil pump pick-up/filter screen assembly.
86 The big-end bearing shells can be renewed without having to remove the cylinder head if the caps are unbolted and the piston/connecting rod pushed gently about one inch up the bore (the crankpin being at its lowest point). If these shells are worn, however, the main bearing shells will almost certainly be worn as well, necessitating a complete overhaul, including crankshaft removal.
87 To remove the piston/connecting rods, the cylinder head must be removed.
88 The big-end caps and their connecting rods are numbered 1, 2, 3 and 4 from the timing cover end of the engine. The numbers are located either side of the rod/cap joint on the engine oil dipstick tube side (photo).
5B.88 Connecting rod and cap numbers
89 Turn the crankshaft as necessary to bring the first connecting rod big-end crankpin to its lowest point, then unscrew the cap bolts and remove the cap and shell bearing.
90 Push the connecting rod/piston assembly up the bore and out of the cylinder block.
There is one reservation; if a wear ridge has developed at the top of the bores, remove this by careful scraping before trying to remove the piston/rod assemblies. The ridge will otherwise prevent removal, or break the piston rings during the attempt.
91 Remove the remaining piston/connecting rods in a similar way. If the bearing shells are to be used again, tape them to their respective caps or rods.
92 Removal of the piston rings and separation of the piston from the connecting rod is covered in the next sub-Section.
93 Fit the bearing shells into the connecting rods and caps, ensuring that the recesses into which the shells seat are clean and dry.
94 Check that the piston ring gaps are evenly spaced at 120º intervals. Liberally oil the rings and the cylinder bores.
95 Fit a piston ring clamp to compress the rings, oiling the rings and the clamp interior surfaces liberally.
96 Insert the first piston/connecting rod into its cylinder bore. Make sure that the assembly is the correct one for its particular bore. The cap and rod matching numbers must be towards the engine oil dipstick guide tube and the arrow on the piston crown towards the timing belt (photo).
5B.96 Piston directional arrow
97 Push the piston into the bore until the piston ring clamp is against the cylinder block and then tap the crown of the piston lightly to push it out of the ring clamp and into the bore (photo).
5B.97 Fitting a piston/connecting rod
98 Oil the crankshaft journal and fit the big-end of the connecting rod to the journal.
Check that the bearing shells are still in position, then fit the big-end cap and bolts; check that the cap is the right way round (photo).
5B.98 Fitting a big-end bearing cap
99 Tighten the big-end bolts to the specified torque (photo). The correct torque is important as the bolts have no locking arrangement. After tightening each big-end, check that the crankshaft rotates smoothly.
5B.99 Tightening a big-end cap bolt
100 Repeat the operations on the remaining piston/rod assemblies.
101 Refit the oil pump pick-up assembly using a new sealing ring.
102 Refit the sump pan and the cylinder head as described in earlier sub-Sections.
103 Fill the engine with oil and coolant.
Pistons/connecting rods -
separation and piston
ring renewal
104 If the piston/connecting rods have been
removed in order to renew the piston rings,
refer to Chapter 1, Section 18, but note that
the piston rings should be fitted so that the
word TOP is uppermost.
105 If new pistons are to be fitted, it is recommended that the gudgeon pins are removed and refitted by a FIAT dealer as the connecting rods must be carefully heated in order to be able to push the gudgeon pin out of the rod small-end, change the piston and push the pin back into position. Locating the gudgeon pin will require a special tool. The gudgeon pin is a sliding fit in the piston but an interference fit in the connecting rod.
106 Refer to Fig. 13.6 for the correct assembly of the piston and connecting rod.
Engine/transmission mountings
- renewal
107 Refer to Chapter 1, Section 33. Three
mountings are used (photos).
5B.107A Left-hand front engine/transmission mounting
5B.107B Left-hand rear engine/transmission mounting
5B.107C Right-hand engine mounting
Fig. 13.5 Piston ring arrangement on the 999 cc engine (Sec 5B)
Fig. 13.6 Piston/connecting rod correctly assembled - 999 and 1108 cc engine
(Sec 5B)
1 Piston grade (A) and directional arrow on piston crown (towards timing
belt)
2 Rod/cap matching numbers
3 Gudgeon pin offset in piston (0.9 to 1.1 mm)
Arrow indicates crankshaft rotation direction
PART C: ENGINE REMOVAL
AND DISMANTLING
Method of removal - general
1 The engine, complete with transmission,
should be removed upwards out of the engine
compartment.
Engine/transmission -
removal and separation
Warning: Refer to the beginning
of Section 9 before starting any
work.
2 Mark the position of the hinges on the underside of the bonnet and then, with the help of an assistant, unscrew the hinge bolts and lift the bonnet to a safe storage area.
3 Drain the coolant; a cylinder block drain plug is not fitted.
4 Drain the engine and transmission oils.
5 Disconnect the battery, negative lead first.
6 Remove the air filter.
7 Disconnect the radiator hoses from the engine (photos).
5C.7A Radiator hose connection to coolant distribution tube
5C.7B Radiator hose at thermostat housing
8 Disconnect the heater hose from the inlet manifold.
9 On fuel injection models, depressurize the fuel system (refer to Section 9D). Disconnect the fuel inlet and return hoses from the fuel pump (photo) or throttle body, as applicable.
5C.9 Fuel hose identification at pump; inlet hose (1), hose to carburettor
(2), return hose (3)
10 Disconnect the brake servo vacuum hose from the inlet manifold.
11 Disconnect the throttle cable from the carburettor, or throttle body as applicable.
12 Disconnect the choke cable, if applicable (photo).
5C.12 Choke cable connection at carburettor
13 Disconnect the leads from the alternator.
14 Disconnect the battery earth lead from the transmission casing.
15 Disconnect the leads from the starter motor and the HT lead from the ignition coil (photo).
5C.15 Ignition coil HT lead connection
16 Disconnect the coolant temperature switch lead and the HT leads from the distributor (photo).
5C.16 Coolant temperature switch
17 Disconnect the lead from the carburettor fuel cut-off (anti-diesel) solenoid valve, where applicable.
18 Disconnect the lead from the oil pressure switch (photo).
5C.18 Oil pressure switch
19 Although not essential, removal of the radiator is recommended as a precaution against its damage during removal of the power unit. Disconnect the wiring plugs from the fan and thermostatic switches (photos).
5C.19A Radiator retaining clip
5C.19B Radiator fan motor wiring connector
5C.19C Radiator fan cut-out thermostatic switch
5C.19D Removing the radiator/fan assembly
20 Disconnect the leads from the reversing lamp switch on the transmission.
21 Disconnect the clutch cable from the release lever on the transmission.
22 Disconnect the speedometer cable from the transmission by unscrewing the knurled ring.
23 Working under the car, disconnect the exhaust downpipes from the manifold and the lower support bracket (photos).
5C.23A Exhaust downpipe flange nuts
5C.23B Unscrewing the exhaust pipe lower support bracket bolt
24 Disconnect the gearchange rods from the levers on the transmission. One rod is retained by a spring clip, the other by a snap-on ball socket. Unbolt the gearchange rod support bracket from the cover plate on the flywheel housing (photos).
5C.24A Gearchange rod connecting pin and spring clip
5C.24B Gearchange rod with ball socket connection
5C.24C Gearchange rod support bracket
25 Remove the screws from the driveshaft inboard gaiter retaining plates (photos).
5C.25A Two of the left-hand driveshaft joint gaiter retaining plate screws
(arrowed)
5C.25B Driveshaft joint gaiter withdrawn
Expect slight oil loss.
26 Disconnect the rear left-hand transmission mounting. Do this by unscrewing the two outer bolts not the centre one. The engine will incline to the rear once the mounting is released (photo).
5C.26 Left-hand rear (lower) transmission mounting disconnected
27 Raise the front of the car and support it securely so that the front roadwheels hang free.
28 Remove the front roadwheels.
29 Unscrew the tie-rod end balljoint taper pin nuts, and then using a suitable “splitter” tool, disconnect the balljoints from the eyes of the steering arms.
30 Unscrew the bolts from the clamps at the bottom of the front suspension struts, tilt the hub carriers outwards and partially disconnect the driveshaft inboard joints from the transmission.
31 Support the weight of the engine/ transmission on a suitable hoist, and then disconnect the right-hand and lefthand front engine/transmission mountings (photos).
5C.31A Right-hand engine mounting disconnected
5C.31B Left-hand engine mounting and bracket
32 Unbolt and remove the engine mounting brackets from the engine and the transmission (photo).
5C.32 Right-hand engine mounting brackets on body and engine
33 Raise the power unit slowly until the driveshafts release from the transmission and can be lowered to rest on the exhaust and bodymember.
34 Continue to raise the engine and the transmission until it can be removed from the engine compartment and placed on the work surface (photo).
5C.34 Lifting out the engine and transmission
35 Clean the exterior of the engine and transmission by steam cleaning or using a water soluble solvent.
36 Unbolt and remove the starter motor.
37 Unscrew the flywheel housing-to-engine flange bolts. Note the location of the engine lifting lug.
38 Unbolt and remove the lower cover plate from the flywheel housing.
39 Pull the transmission from the engine. It is located by two hollow dowels and one stud (photo).
5C.39 Separating the engine and transmission
Dismantling - general 40 Refer to Chapter 1, Section 14.
Complete dismantling
Warning: Refer to the beginning
of Section 9 before starting any
work.
41 Unbolt and remove the camshaft cover.
42 Unbolt and remove the timing belt cover.
43 Remove the distributor (Section 10).
44 Remove the hot air collector and the exhaust manifold.
45 Release, disconnect and remove the coolant distribution pipe from the rear of the coolant pump.
46 Unscrew and discard the oil filter cartridge.
47 Unbolt the thermostat housing, discard the joint gasket.
48 Remove the fuel pump, together with its insulator block and actuating pushrod, if applicable.
49 Remove the carburettor, or throttle body, as appropriate.
50 Remove the inlet manifold and discard the joint gasket.
51 Remove the alternator and its drivebelt and withdraw the engine oil dipstick.
52 Unbolt and remove the crankshaft pulley.
53 Unbolt and remove the timing belt tensioner.
54 Remove the timing belt.
55 Unbolt and remove the coolant pump.
56 Remove the cylinder head.
57 Remove and discard the cylinder head gasket.
58 Remove the clutch.
59 Lock the flywheel starter ring gear teeth and remove the crankshaft sprocket bolt and sprocket.
60 Unbolt and remove the sump pan, then the exhaust pipe support bracket (photos).
5C.60A Removing the sump pan
5C.60B Exhaust pipe support bracket attached to crankcase
61 Prevent rotation of the crankshaft by locking the starter ring gear teeth and then unbolt and remove the flywheel. The flywheel can only be fitted in one position as it is located on a dowel.
62 Remove the engine rear plate. Note the small socket-headed screw which holds the timing index plate (photo).
5C.62 Unscrewing socket-head screw from timing index plate
63 Unbolt and remove the oil pump pick-up assembly, followed by the oil pump itself.
64 Turn the engine on its side and remove the piston/connecting rod assemblies.
65 Stand the engine on its cylinder block machined face, and then unbolt and remove the crankshaft rear oil seal retainer. Discard the gasket.
66 Note the markings on the main bearing caps. One line on the cap nearest the timing belt, then two, C for centre cap, then three and four (photo).
5C.66 Main bearing cap markings
67 The caps will only fit one way round.
68 Unbolt the main bearing caps, removing them with the shell bearings.
69 Lift the crankshaft from the crankcase and remove the bearing half shells from the crankcase. If the shells are to be used again, keep them with their respective bearing caps.
70 The thrust washers which control crankshaft endfloat are located in the crankcase, and retained by the turned-over edges of the centre main bearing shell.
71 The engine is now fully stripped.
Examination and renovation 72 The procedures for the following items are essentially as described in Chapter 1, Section 18.
Cylinder block and crankcase
Crankshaft and bearings
Flywheel
Oil seals and gaskets
Cylinder head
73 Using a straight-edge, check the cylinder
head gasket surface for distortion. If it
exceeds the specified tolerance, it must be
surface ground by your dealer.
74 Refer to Chapter 1, Section 39, for dismantling and renovation operations. Note that single valve springs are fitted.
Oil pump
75 Checking operations are described in
sub-Section B.
Pistons and connecting rods 76 Refer to sub-Section B.
77 If one or more connecting rods are changed, it is important that its weight is identical to that of the original. Use an accurate balance to weigh them and remove metal if necessary from the new rod in the areas indicated in Fig. 13.7.
Camshaft and cam followers 78 If the camshaft journals or bearings show any sign of wear or scoring, then the camshaft, or cylinder head, or both must be renewed.
79 The cam followers should be checked for ovality using a micrometer. Unless unworn they should be renewed.
Timing belt tensioner and timing belt 80 The tensioner is a lubricant-sealed pulley, and it should be tested for smooth and quiet operation by turning it with the fingers. Any evidence of roughness or rattle will indicate the need for a new assembly (photo).
5C.80 Timing belt tensioner
81 The timing belt should be inspected at regular intervals for correct adjustment and condition (see Section 3 or “Routine maintenance” at the beginning of the Manual).
If there is evidence of worn teeth, cracking or fraying, or oil contamination, renew the belt.
The vehicle manufacturers recommend that the belt is renewed whenever it is removed, and it should certainly be renewed at the intervals specified in Section 3 or the main “Routine maintenance” section at the beginning of this Manual as a precautionary measure against belt breakage and consequent expensive engine damage.
Fig. 13.7 Metal removing areas (arrowed) on connecting rod - 999 and 1108 cc
engine (Sec 5C)
Fig. 13.8 Checking a cam follower for ovality - 999 and 1108 cc engine (Sec
5C)
PART D:
ENGINE REASSEMBLY AND
REFITTING
Reassembly - general
1 Refer to Chapter 1, Section 19.
Complete reassembly
2 With the cylinder block/crankcase standing
on the work surface, fit the bearing half shells
into their crankcase seats (photo). Make sure
that the seats are perfectly clean as dirt or grit
trapped under the shell will cause binding
when the crankshaft is turned.
5D.2 Main bearing shell in crankcase
3 The centre bearing crankcase web incorporates the thrust washers held by the lips of the bearing shell (photo).
5D.3 Crankshaft thrust washer at centre bearing
4 Oil the shells and lower the crankshaft into the crankcase (photo).
5D.4 Fitting the crankshaft
5 Fit the bearing shells into the main bearing caps, again making sure that the shell seats are perfectly clean (photo).
5D.5 Main bearing cap and shell
6 Fit the main bearing caps in their numbered sequence and the correct way round (photo).
5D.6 Fitting a main bearing cap
7 Clean the threads of the main bearing cap bolts, lightly oil them and screw them in finger-tight. Tighten all bolts progressively to the specified torque, then check that the crankshaft turns smoothly and evenly (photos).
5D.7A Initial tightening of a main bearing cap bolt
5D.7B Angle-tightening a main bearing cap bolt
8 Now check the crankshaft endfloat. Do this using a dial gauge or feeler blades inserted between the machined shoulder of a journal and the side of the bearing cap (photo). Move the crankshaft fully in one direction and then the other to ensure that full movement is obtained. If the endfloat is outside the specified tolerance and new bearing shells have been fitted, then a fault must have occurred during crankshaft regrinding.
5D.8 Checking crankshaft endfloat using a dial gauge
9 Fit a new oil seal to the crankshaft rear oil seal retainer. Apply grease to the seal lips. A conventional gasket is not used at the oil seal joint face but a 3.0 mm diameter bead of RTV silicone instant gasket must be applied to a clean surface as shown in Fig. 13.9 (photo).
5D.9 Fitting crankshaft rear oil seal retainer
10 Bolt the retainer into position. One hour at least must be allowed for the RTV to cure before oil contacts it.
11 Turn the engine on its side and fit the piston/connecting rods as described in sub-Section B.
12 Fit a new oil seal to the oil pump, oil the seal lips and bolt on the pump using a new joint gasket (photos).
5D.12A Oil pump gasket
5D.12B Tightening an oil pump bolt
13 Use a new sealing washer and fit the oil pick-up/filter screen assembly.
14 Fit the engine rear plate and then the flywheel on its mounting flange. Apply thread-locking fluid to (clean) bolt threads and screw in the bolts to the specified torque (photo). Hold the flywheel against rotation by locking the starter ring gear with a suitable tool.
5D.14 Tightening a flywheel bolt
15 Fit the sump pan as described in sub-Section B.
16 Fit the crankshaft sprocket so that the timing mark is visible. Lock the flywheel starter ring gear teeth, and screw in and tighten the sprocket bolt to the specified torque (photos).
5D.16A Crankshaft sprocket showing integral key
5D.16B Tightening the crankshaft sprocket bolt
17 Refit the clutch to the flywheel as described in Chapter 5. Make sure that the driven plate is centralised.
18 Fit the cylinder head.
19 Refit the coolant pump. A conventional gasket is not used at the joint face, but apply a continuous bead of RTV silicone instant gasket 3.0 mm in diameter to the pump mating surface. Allow at least one hour for curing before permitting coolant to contact it.
20 Fit the timing belt rear cover, then the timing belt tensioner and lock in its retracted position (photo).
5D.20 Fitting the timing belt rear cover
21 Fit and tension the timing belt as described in sub-Section B.
22 Bolt on the crankshaft pulley (photo).
5D.22 Crankshaft pulley installation
23 Refit the alternator and drivebelt (photo).
5D.23 Alternator and drivebelt
24 Refit the engine oil dipstick.
25 Using a new gasket, bolt on the inlet manifold, tightening the nuts to the specified torque (photos).
5D.25A Inlet manifold gasket
5D.25B Fitting the inlet manifold
26 Refit the carburettor, or throttle body, as appropriate.
27 Fit the fuel pump, insulator block and actuating rod, if applicable. Make sure that a new gasket is placed on each side of the pump insulator block.
28 Using a new gasket, bolt on the thermostat housing.
29 Oil the sealing ring of a new oil filter cartridge and screw it into position using hand pressure only (photo).
5D.29 Oil filter cartridge and mounting base
30 Refit the coolant distribution pipe to the rear of the coolant pump. Use a new seal (photo).
5D.30 Coolant distribution pipe
31 Using a new gasket, bolt on the exhaust manifold (photo).
5D.31 Exhaust manifold
32 Fit the hot air collector plate for the air cleaner (photo).
5D.32 Air cleaner hot air collector plate
33 Refer to Section 10 and fit the distributor.
34 Bolt on the timing belt cover.
35 Fit the camshaft cover, using a new gasket unless the original one is in perfect condition.
Engine/transmission -
reconnection and refitting
36 Locate the engine in an upright position
on wooden blocks to allow for the greater
depth of the transmission flywheel housing
when it is joined to the engine.
37 Make sure that the clutch driven plate has been centralised, offer the transmission to the engine and locate the flywheel housing on the single stud and dowels.
38 Tighten the connecting bolts to specified torque, having located the lifting eye (photo).
5D.38 Lifting eye on flywheel housing flange
39 Bolt on the starter motor.
40 Refit the cover plate to the flywheel housing, but do not insert the lower bolts at this stage as they retain the support bracket for the gearchange rod.
41 The engine and transmission are now ready for refitting. The operations are a direct reversal of the operations described earlier, but observe the following points.
42 Have the engine/transmission perfectly horizontal and suspended on the hoist.
43 Lower it into position very slowly until it is possible to engage the driveshaft inboard joints with the transmission.
44 Continue lowering until the driveshafts can be fully engaged and the mountings reconnected. Remove the hoist.
45 Tighten all nuts and bolts to the specified torque. Note the method shown for connecting the gearchange rod ball socket using pliers (photo).
5D.45 Connecting ball socket type gearchange rod
46 Refill the engine with oil and coolant and replenish the transmission oil.
Initial start-up after major
overhaul
47 Refer to Chapter 1, Section 45.
Fig. 13.9 Application area for silicone gasket on crankshaft rear oil seal
retainer (Sec 5D)




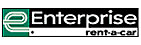
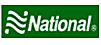

