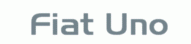
Fiat Uno Manual
Engine - complete reassembly (1116 cc and 1301 cc engines)Engine / Engine - complete reassembly (1116 cc and 1301 cc engines)
Crankshaft and main bearings 1 Fit the bearing shells to their crankcase seats and to their caps. The seatings and backs of the shells must be spotlessly clean, otherwise tight spots will occur when the crankshaft is fitted. The centre bearing shell is plain (photo).
42.1 Main bearing shells
2 Fit the thrust washer halves to their locations at No. 5 bearing, noting that the oil grooves in the washers face outwards (photo).
42.2 Crankshaft thrust washers
3 Oil the surfaces of the bearing shells liberally and lower the crankshaft into position (photo).
42.3 Lowering crankshaft into position
4 Fit the main bearing caps to their correct locations, the correct way round (numerical chisel marks towards the auxiliary shaft). The rear cap is unmarked. Tighten the cap bolts to the specified torque (photos).
42.4A Number one main bearing cap
42.4B Tightening a main bearing cap bolt
5 Check that the crankshaft rotates smoothly and freely.
6 At this stage, the crankshaft endfloat should be checked. Prise the crankshaft fully in one direction and measure the gap between the machined face of the flywheel mounting flange and the crankcase. Now push the shaft in the opposite direction and measure again. Ideally, a dial gauge should be used for these measurements, but feeler blades will serve as a reasonable alternative.
The difference between the two dimensions (feeler blades) or the total movement of the crankshaft (dial gauge) should be within the specified tolerance. If it is not, the thrust washers at No. 5 main bearing will have to be changed for thicker ones; this will require taking out the crankshaft again to reach them.
7 Fit new oil seals to the retainers and, using new gaskets, bolt the retainers to the front and rear ends of the crankshaft, having first filled the oil seal lips with grease (photos).
42.7A Removing oil seal from carrier
42.7B Front oil seal carrier
42.7C Rear oil seal carrier
Pistons/connecting rods 8 The refitting operations are described in Section 32.
Auxiliary shaft
9 Lubricate the auxiliary shaft bearings and fit
the shaft into the crankcase (photo).
42.9 Fitting the auxiliary shaft
10 Fit a new seal to the endplate and fit the plate to the crankcase, using a new gasket (photos).
42.10A Auxiliary shaft end plate and gasket
42.10B Tightening auxiliary shaft end plate bolt
11 Fit the belt sprocket and partially tighten its bolt. Then, using an oil filter strap wrench or similar device to hold the sprocket against rotation, tighten the bolt to the specified torque. Take care not to damage the teeth of the sprocket, which is of fibre construction (photo).
42.11 Tightening camshaft sprocket bolt. Note sprocket locking device
Oil sump, sump pan and
breather
12 Fit the oil drain pipe by tapping it into
place, squarely in its hole in the crankcase.
Tighten its retaining bolt (photo).
42.12 Tightening oil drain pipe bolt
13 Bolt up the oil pump, using a new gasket at its mounting flange (photo).
42.13 Locating oil pump and gasket
14 Fit the sump (using a new gasket) and tighten the securing screws to the specified torque. Note the reinforcement washers (photo).
42.14 Tightening sump pan bolt
15 Insert the oil pump/driveshaft into the distributor hole. This does not have to be specially positioned as the distributor is splined to the shaft and can be set by moving its location in the splines (refer to Chapter 4) (photo).
42.15 Fitting oil pump driveshaft
16 Push the breather into its crankcase recess and tighten its securing bolt (photos).
42.16A Crankcase breather seal
42.16B Crankcase breather and retaining bolt
Flywheel, crankshaft sprocket
and pulley
17 Make sure that the flywheel-to-crankshaft
mounting flange surfaces are clean. Although
the bolt holes have unequal distances
between them, it is possible to fit the flywheel
in one of two alternative positions at 180º
difference. Therefore if the original flywheel is
being refitted, align the marks made before
removal.
18 If a new flywheel is being fitted, or if alignment marks were not made before dismantling, set No. 1 position at TDC (crankshaft front Woodruff key pointing vertically). Fit the flywheel to its mounting flange so that its timing dimple is uppermost and in alignment with the relative position of the TDC mark on the flywheel housing inspection window.
19 Insert the bolts and tighten them to the specified torque, jamming the ring gear to prevent the flywheel turning. Fit the engine endplate (photo).
42.19 Tightening flywheel bolts
20 Fit the timing belt sprocket to the front end of the crankshaft (photo).
42.20 Fitting crankshaft timing belt sprocket
21 Fit the crankshaft pulley and the nut; tighten it to the specified torque, again jamming the starter ring gear to prevent the crankshaft from rotating (photo).
42.21 Crankshaft pulley and nut
Cylinder head
22 Refitting is described in Section 29.
Camshaft carrier and camshaft 23 Refitting is described in Section 27.
Timing belt and tensioner 24 Refitting is described in Section 28, but make sure that the belt cover rear plate is bolted into position. If the engine mounting bracket was removed, bolt it into position complete with the tensioner plunger to provide spring pressure to the belt pulley (photos).
42.24A Belt cover rear plate
42.24B Belt cover mounting stud
42.24C Engine mounting bracket with belt tensioner plunger (arrowed)
Valve clearances
25 Check the valve clearances as described
in Section 26.
26 Using new gaskets, bolt on the camshaft carrier cover plate and the inlet and exhaust manifolds using new gaskets. Fit the exhaust manifold hot air collector plate (photo).
42.26 Tightening a camshaft carrier cover nut
27 Locate the engine rear plate on its dowels by sliding it behind the flywheel (photo).
42.27 Engine rear plate




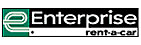
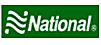

